Power density, RDS(on) and miniaturization
通过大量投资于研发,我们持续不断地利用先进的小信号和功率MOSFET解决方案扩充我们的产品组合。我们种类齐全的产品组合提供当今市场所需的灵活性,让您可以轻松选择最适合您系统的产品。我们市场领先的技术确保提供最高的可靠性和性能,而先进的封装则可以增强电阻和热性能,同时缩小尺寸,降低成本。
精选产品
Focus Packages
最新新闻和博客
参数搜索

Get MOSFETs suggested based on your application
With over 900 products in our portfolio – you don’t need to be an expert in MOSFETs to select the device with the best performance for your requirements. Specify your application below, put in your conditions and get three MOSFETs suggested. The suggestions are based on results from spice simulations with the top three best performing devices shown.
Application note (31) |
|||
---|---|---|---|
文件名称 | 标题 | 类型 | 日期 |
AN50003.pdf | Driving solenoids in automotive applications | Application note | 2025-04-09 |
AN11243.pdf | Failure signature of Electrical Overstress on Power MOSFETs | Application note | 2025-03-20 |
AN11158.pdf | Understanding power MOSFET data sheet parameters | Application note | 2025-02-18 |
AN90011.pdf | Half-bridge MOSFET switching and its impact on EMC | Application note | 2025-02-10 |
AN90001.pdf | Designing in MOSFETs for safe and reliable gate-drive operation | Application note | 2024-10-28 |
AN11160.pdf | Designing RC Snubbers | Application note | 2024-10-21 |
AN50020.pdf | MOSFETs in Power Switch applications | Application note | 2024-05-27 |
AN90034.pdf | Nexperia Precision Electrothermal models in SPICE and VHDL-AMS for Power MOSFETs | Application note | 2024-04-30 |
AN50019.pdf | Thermal boundary condition study on MOSFET packages and PCB substrates | Application note | 2024-04-15 |
AN90003.pdf | LFPAK MOSFET thermal design guide | Application note | 2023-08-22 |
AN50005_translated_20230317.pdf | 大電力アプリケーションにおけるパワーMOSFETの並列接続 | Application note | 2023-04-03 |
AN50009.pdf | Power MOSFET applications in automotive BLDC and PMSM drives | Application note | 2022-07-05 |
AN10273.pdf | Power MOSFET single-shot and repetitive avalanche ruggedness rating | Application note | 2022-06-20 |
AN50006.pdf | Power MOSFETs in linear mode | Application note | 2022-04-12 |
AN50014.pdf | Understanding the MOSFET peak drain current rating | Application note | 2022-03-28 |
AN90032.pdf | Low temperature soldering, application study | Application note | 2022-02-22 |
AN50005.pdf | Paralleling power MOSFETs in high power applications | Application note | 2021-09-13 |
AN50002.pdf | Automotive LED side light SEPIC DC-to-DC converter design example | Application note | 2021-05-10 |
AN11261.pdf | RC Thermal Models | Application note | 2021-03-18 |
AN50001.pdf | Reverse battery protection in automotive applications | Application note | 2021-01-12 |
AN11158_ZH.pdf | Understanding power MOSFET data sheet parameters | Application note | 2021-01-04 |
AN11156.pdf | Using Power MOSFET Zth Curves | Application note | 2021-01-04 |
AN90023.pdf | Thermal performance of DFN packages | Application note | 2020-11-23 |
AN90016.pdf | Maximum continuous currents in NEXPERIA LFPAK power MOSFETs | Application note | 2020-09-03 |
AN90017.pdf | Load switches for mobile and computing applications | Application note | 2020-09-02 |
AN90019.pdf | LFPAK MOSFET thermal resistance - simulation, test and optimization of PCB layout | Application note | 2020-07-20 |
AN10441.pdf | Level shifting techniques in I2C-bus design | Application note | 2020-02-11 |
AN90009.pdf | Leakage of small-signal MOSFETs | Application note | 2019-11-08 |
AN11599.pdf | Using power MOSFETs in parallel | Application note | 2016-07-13 |
AN11119.pdf | Medium power small-signal MOSFETs in DC-to-DC conversion | Application note | 2013-05-07 |
AN11304.pdf | MOSFET load switch PCB with thermal measurement | Application note | 2013-01-28 |
Leaflet (18) |
|||
文件名称 | 标题 | 类型 | 日期 |
nexperia_document_CCPAK-MOSFETs_2024_Chinese.pdf | CCPAK MOSFET LEAFLET CN | Leaflet | 2024-12-02 |
nexperia_document_CCPAK_MOSFETs_2024.pdf | Nexperia CCPAK MOSFETs | Leaflet | 2024-11-19 |
nexperia_document_leaflet_IDs_2024_CHN.pdf | nexperia_document_leaflet_IDs_2024_CHN | Leaflet | 2024-09-12 |
nexperia_document_leaflet_IDs_2024.pdf | nexperia_document_leaflet_IDs_2024 | Leaflet | 2024-09-12 |
nexperia_document_leaflet_DFN_Packages_Diodes_Transistors_ESD_Protection.pdf | DFN Packages Diodes Transistors ESD Protection | Leaflet | 2024-08-26 |
nexperia_document_leaflet_DFN2020MD-6_2023.pdf | DFN2020MD-6 Leadless package with side-wettable flanks | Leaflet | 2023-09-19 |
nexperia_document_leaflet_DFN2020MD-6_2023-CHN.pdf | 带有侧边可湿焊盘的无引脚封装 | Leaflet | 2023-09-19 |
nexperia_document_leaflet_SsMOS_for_mobile_2022.pdf | High volume small-signal MOSFETs for mobile and portables, in WLCSP and leadless DFN packages | Leaflet | 2022-07-04 |
nexperia_document_leaflet_SsMOS_for_mobile_2022-CHN.pdf | 适合移动和便携式设备的 大批量小信号MOSFET, 采用WLCSP和无引脚DFN封装 | Leaflet | 2022-07-04 |
nexperia_document_leaflet_LFPAK88_2022_CHN.pdf | LFPAK88 将功率密度提升到新高度 | Leaflet | 2022-03-10 |
nexperia_document_leaflet_LFPAK88_2022.pdf | LFPAK88 - Driving power-density to the next level | Leaflet | 2022-03-09 |
nexperia_document_leaflet_DFN0606_LR_2020.pdf | DFN0606 | Leaflet | 2020-04-15 |
nexperia_document_leaflet_DFN0606_CHN_2020.pdf | DFN0606 Chinese Translation | Leaflet | 2020-04-15 |
Nexperia_Document_Leaflet_LFPAK33_12022020_CH.pdf | LFPAK33 leaflet | Leaflet | 2020-03-25 |
Nexperia_Document_Leaflet_LFPAK33_12022020.pdf | LFPAK33 shrinking the power footprint | Leaflet | 2020-03-25 |
nexperia_document_leaflet_WLCSP_201803_CHN.pdf | WLCSP Chinese Translation | Leaflet | 2018-04-25 |
nexperia_document_leaflet_WLCSP_201803.pdf | Small-signal MOSFETs in WLCSP - Smallest size - lowest RDS(on) | Leaflet | 2018-04-25 |
nexperia_document_leaflet_LFPAK56D_factsheet_LR_201708.pdf | LFPAK56D the ultimate dual MOSFET | Leaflet | 2017-08-17 |
Marcom graphics (1) |
|||
文件名称 | 标题 | 类型 | 日期 |
LFPAK56_SOT669_mk.png | plastic, single-ended surface-mounted package; 4 terminals; 4.9 mm x 4.45 mm x 1 mm body | Marcom graphics | 2017-01-28 |
Selection guide (2) |
|||
文件名称 | 标题 | 类型 | 日期 |
Nexperia_Selection_Guide_2025.pdf | Nexperia selection guide 2025 | Selection guide | 2025-03-26 |
Nexperia_Selection_guide_2023.pdf | Nexperia Selection Guide 2023 | Selection guide | 2023-05-10 |
Technical note (3) |
|||
文件名称 | 标题 | 类型 | 日期 |
TN90002.pdf | H-bridge motor controller design using Nexperia discrete semiconductors and logic ICs | Technical note | 2025-02-10 |
TN00008.pdf | Power MOSFET frequently asked questions and answers | Technical note | 2024-08-09 |
TN90001.pdf | LFPAK MOSFET thermal resistance Rth(j-a) simulation, test and optimisation of PCB layout | Technical note | 2018-05-17 |
User manual (3) |
|||
文件名称 | 标题 | 类型 | 日期 |
Nexperia_document_book_MOSFETGaNFETApplicationHandbook_2020.pdf | MOSFET & GaN FET Application Handbook | User manual | 2020-11-05 |
The_Power_MOSFET_Handbook_Chinese_Version_201808.pdf | The Power MOSFET Handbook - Chinese Version 201808 | User manual | 2019-11-12 |
UM90001.pdf | Store and transport requirements | User manual | 2018-04-06 |
White paper (1) |
|||
文件名称 | 标题 | 类型 | 日期 |
Nexperia_document_whitepaper_DFN_Wave_Soldering_2020.pdf | Whitepaper: Can DFNs be successfully wave soldered? | White paper | 2020-09-01 |
常见问题
Trench 6逻辑电平MOSFET的10 V VGS额定值是由我们小于1 ppm的故障率目标决定的,这在当时被评为最佳行业惯例。ppm故障系数未在任何数据手册中给出,也不属于AEC-Q101质量标准的一部分。换言之,两种器件可能都符合AEC-Q101标准,但仍然具有不同的ppm故障率系数。
定义、表征和保护这些额定值的方法得到了改进,现在有可能在超过给定的10 V额定值的条件下工作。这将表示为时间、电压和温度的函数。进一步说明见下文;更多详细信息请参阅Nexperia应用笔记AN90001。
附加信息
上述问题中有两个关键词值得进一步探讨——“额定值”和“逻辑电平”。
逻辑电平MOSFET主要用于驱动电压为5 V的应用
并据此进行了相应优化。为了在相对较低的栅极电压下实现全导通MOSFET和最佳导通电阻性能,这些MOSFET需要比以10 V VGS驱动的标准电平器件更薄的栅极氧化层。更薄的栅极氧化层会在较低的电压下击穿,并且具有比标准电平更低的额定值(完整详情请参阅AN90001第5节)。
但是在某些情况下,会为非逻辑电平应用选择逻辑电平MOSFET。例如,在汽车应用中,电池电源电压可能下降到驱动电路需要在6 V以下工作的水平。因此,MOSFET必须以低于标准电平MOSFET能够提供的栅极电压导通。相反,MOSFET栅极需要耐受约为12 V的标称电池电压。
逻辑电平MOSFET适合吗?
就性能而言,逻辑电平MOSFET不会在施加较高电压时突然发生故障。但是,施加高于最大额定电压的VGS会使小于1 ppm的故障率升高,因此Nexperia不会考虑在数据手册中包含这些额定值。
通过在生产过程中进行有效筛选,Nexperia消除缺陷并减少早期使用寿命故障的方法得以实现。作为供应商,Nexperia致力于实现零缺陷和高质量水平。因此,额定值可能会低于我们的竞争对手,他们对质量的承诺可能不那么严格。Nexperia VGS的最大额定值基于在175℃下施加100%的最大(额定)电压1000小时,故障率小于1 ppm——更多详细信息请参阅:AN90001第4节。
当数据手册中的VGS额定为±20 V时,设计人员必须考虑逻辑电平MOSFET的故障率系数
Nexperia有一个模型,可用于计算较高的栅极电压随温度变化的使用寿命故障率。此信息可根据要求以所计算系数的形式提供,仅供参考。
与前几代产品一样,额定值是基于满足AEC-Q101要求而提出的。但是,Nexperia开发了一种新的测试方法,可确保在额定VGS下,整个使用寿命内故障率小于1 ppm。这已应用于Trench9,其VGS额定值已设置为满足这一新要求。
附加信息
详细说明请参阅AN90001
在Trench第3代器件(2008年)和Trench第6代器件(2012年)之间,Zth曲线的设置方法改变了。芯片尺寸也不同,这改变了Zth和Rth特性。
附加信息
较早的方法使用Zth (1 μs)和Rth的经验模型以及指数线。
最新方法使用计算流体动力学(CFD)仿真生成的Zth模型,经过了测量验证。
两个器件中的芯片尺寸不同,因此Zth也不同。
图1所示的曲线比较了单次Zth的数据手册曲线。
两个器件的极值线非常匹配。最大的差异是1 ms到20 ms之间的区域。
通过比较得出的结论是,Trench第3代器件用于在这些Zth限值内工作。Trench第6代器件是一个很好的替代方案,极有可能满足工作要求。
可以评估如何使用新规则对Trench第3代器件进行评级,以更准确地反映其真实性能。图1表示两条数据手册线对比后的新线。
虽然在Rth上有一处差异,但可能并不重要。实际上,这是Rth(j-amb),是设计的限制因素。两个器件的共性是印刷电路板(PCB)的Rth,占主导地位。
考虑BUK9Y30-75B的新旧测试方法时,另一个差异是小于10 μs的区域。
对于1 μs和2 μs之间的脉冲持续时间,Trench第3代器件中的温升(或Zth(j-mb))仅为原始数据手册曲线预测值的一半。这个因素的重要性取决于应用。
这种理解是正确的。为确保MOSFET的可靠性,请始终将最高结温限制在175 ℃。
附加信息
据了解,数据手册中列出的典型热阻值是基于受控条件得出的,不适用于典型应用。
在半导体行业中,结温为25 ℃的器件特性是公认标准。用户在这个温度下进行测量也最方便。
如何计算正确的热阻?
Nexperia的MOSFET数据手册中仅给出了热阻的最大值。典型值远小于最大值。据了解,热循环会导致Rth(j-mb)在MOSFET使用寿命期间增加。
数据手册Rth(j-mb)最大值中包含了公差裕度,允许该值在MOSFET的使用寿命期间增加。
对于最坏情况的设计分析,请始终使用最大值。数据手册中给出的最大Rth(j-mb)是通过特性测量评估得出。
其值不受温度或其他环境条件限制。
如何计算结温?
由于环境和/或MOSFET中的功耗引起的温升,MOSFET通常在结温高于25 ℃的情况下工作。
如果已知MOSFET的功耗和贴装基底温度(Tmb),就可以计算MOSFET的结温。使用下面的公式(1)确定Tj。
(1) Tj = P × Rth(j-mb) + Tmb
MOSFET的SPICE热模型提供了一种通过仿真估算Tj的好方法。在MOSFET的功耗随时间变化时尤为有用。
BUK7Y12-40E的实例:
来自数据手册:
25 ℃时的最大RDSon = 12 mΩ
175 ℃时的最大RDSon = 23.6 mΩ
2.31 K/W时的最大Rth(j-mb)
来自应用数据:
PWM频率 = 100 Hz
最大占空比 = 50 % Vsupply = 14 V
Rload = 0.7 Ω
最高环境温度 = 85 ℃
最高PCB温度 = 100 ℃
基于平均功率计算,忽略因功率脉冲引起的任何温度波动,也忽略100 Hz时的开关损耗:
假设MOSFET的初始温度为100 ℃,其最大导通电阻为18 mΩ。它处于25 ℃时的12 mΩ和175 ℃时的24 mΩ之间。
传导时,MOSFET功耗I2 X RDSon为:20 x 20 x 0.018 = 7.2 W
占空比为50%,因此平均功耗 = 7.2 x 0.5=3.6 W。假定可以忽略100 Hz时的开关损耗。
MOSFET结温升高(贴装基底以上)为:2.31 x 3.6 = 8.3 K。
在这种情况下,MOSFET的最高芯片温度非常安全,为:100 + 8.3 = 108.3 ℃
为确保PCB温度在85 ℃的环境中不会升高到100 ℃以上,PCB与环境之间的热阻必须为:(100 - 85)/3.6 = 4.2 K/W
The customer is trying to achieve a Rth(j-amb) = 60 K/W using a dual N channel LFPAK56 (SOT1205).
Rth(j-amb) = Rth(j-mb) + Rth(mb-amb)
Rth(j-mb) is in Nexperia’s control (it is a function of the die size and package design, for example the bigger the die the lower the Rth(j-mb)). Rth(mb-amb) is a function of the PCB design and the thermal management scheme and is not under the control of Nexperia. A very good multilayer FR4 design with thermal vias would be around 30 - 40 K/W.
The Rth(j-amb) is dependent on the PCB design. As MOSFET manufacturers we do not determine this part of the system and the value would be meaningless, therefore. We have provided some examples in our application notes, please see LFPAK thermal design guide AN90003.
Rth(j-mb) tells you the temperature difference between the junction and mounting base for a given power profile. Because of the power dissipation the mounting base to ambient path will also heat up, causing the junction temperature to rise further. The junction to ambient is the full thermal path that needs to be considered and is a function of the PCB design too, please see AN90003 for more details.
The drain tab (mounting base) and source leads are the two main paths through which a down side cooling package dissipates heat. In fact, contrarily to some through hole packages (like TO-220), SMD packages such as LFPAK and D2PAK get rid of all the heat through the PCB. Hot air rises from the board and envelopes the device lowering the efficiency and thus the efficacy of any heatsink attached to the top of the plastic case. Instead, when a substantial power needs to be dissipated, copper traces, vias and planes are employed in order to lower as much as possible the Rth(j-a) of a device.
FloTHERM simulations and measurements carried out using LFPAK56 and variable power dissipation and PCB copper area show how, in steady state conditions, temperature taken on the top center of the case is, within a reasonably low accuracy, very similar to the junction temperature. This result is not due to heat being dissipated from the top of the case but rather from the one coming out of the PCB that increases the temperature of the surrounding air immediately close to the device, up to almost that of the junction.
Conduction is the predominant phenomena regulating heat flow from junction to mounting base. The resulting resistance is inversely proportional to the cross sectional area of the medium through which it propagates (die area) and directly to its thickness (drain tab). Given an LFPAK56E and an LFPAK88 with the same die size the former has lower Rth(j-mb) because the thickness of its drain tab is lower. It is worth noting, however, that the thermal path doesn't end here and that the LFPAK88 shows better thermal performances due to its lower Rth(j-amb) given by a much larger drain tab.
For a given die size the LFPAK88 shows an overall better transient thermal impedance Zth(j-mb).
The data sheet states the IS capability for the diode. The power constraints are the same as for the MOSFET conduction. The diode is an integral part of the MOSFET structure. They are in effect the same size and have the same thermal properties. The MOSFET can carry the same current through the channel or in reverse through the body diode. The maximum steady state current in the diode is dependent on the total allowed power loss for the device. However, the diode current may be different from the channel current because the power dissipation may be different under the 2 modes of operation.
When a MOSFET transitions from diode conduction to blocking state there is an additional loss, called the diode recovery charge (Qr). The Qr needs to be factored in the switching loss calculation of the application for accurate analysis. This switching transition also impacts on the EMC performance and needs careful consideration - see AN90011 and TN90003 for more details.
The most important factor in current derating or power derating is junction temperature. Tj is a function of power dissipation. Power dissipation is a function of ID current and on-state resistance (P = I^2 × R) when operating in the fully enhanced mode. It is the product of ID and VDS when operating between on and off states. The RDS(on) of a MOSFET, increases with increase in temperature. Therefore, for a given maximum power dissipation, the maximum current must be derated to match the maximum power dissipation. In Nexperia data sheets, graphs show the continuous drain current and normalized total power dissipation as a function of the mounting base temperature. These graphs can be used to determine the derating.
If current, voltage, power, junction temperature, etc. are within Nexperia data sheet limitations, no additional derating is needed. In the data sheet, there is a power derating curve based on junction temperature. Junction temperature (Tj) is one of the most important factors for reliability. Particular care should be taken to extract enough heat from the device to maintain junction or die temperature, below rated values. The device should be operated within the SOA region. It should be de-rated if necessary as recommended in the data sheet and it should be possible to obtain optimum reliability.
As an example, assume that the temperature required is 100 °C, instead of 25 °C. Tj rated is 175 °C for this automotive grade MOSFET. To de-rate when considering the effect of temperature on SOA performance the current must be reduced. To determine the new current (at temperature) for a fixed voltage, use the power derating line. For example, power at 100 °C = 50 % of power at 25 °C. Therefore, the 1.0 A line represents 0.5 A at 100 °C etc. It is explained in Application Note AN11158. If necessary, the SOA lines for 1 ms, 10 ms etc. can be extended at the same slope to the right.
The Spirito region or hot spotting issue with new higher density technologies may have more effect in the linear mode of operation. This effect is evident from the change in gradient in the limit lines for 1 ms, 10 ms and 100 ms at higher VDS values. The 1 ms, 10 ms, 100 ms and DC lines at higher VDS values emphasize it. The reason is that most newer technologies pack more parallel fundamental cells to share more current in a smaller die (lower RDS(on) per unit area). It leads to an increased thermal coupling between cells. Also, to attain higher current densities, the MOSFETs are designed with higher transconductance or gain (gfs = ID/VGS). It enables them to carry higher currents even at lower VGS values. However VGS(th) (threshold voltage) has a negative temperature coefficient which leads to a higher zero temperature coefficient crossover value. For various reasons, the distribution of temperature in the die is never perfectly uniform. Therefore, when the device is operated for extended periods in linear mode, hot spotting occurs. Due to the shift in threshold voltage, there is a risk of thermal runaway and device destruction where the hotspots form. Because of these reasons, special care should be taken when using trench or planar MOSFETs for linear applications. Ensure that operation remains within the data sheet SOA limits.
The inflexion points on the 1 ms and 10 ms lines represent the points where the ‘Spirito’ effect starts. At higher ID, the lines represent constant power (P); at lower ID, P decreases as ID
decreases. The 100 ms and DC lines are straight, but have higher negative gradients than constant power lines, i.e. power also decreases as ID decreases. The flat portion of the DC line represents package maximum ID.
The Spirito effect is a form of electro-thermal instability i.e. uneven die heating leading to hot-spot formation. It happens because VGS(th) has a Negative Temperature Coefficient (NTC) at ID values below IZTC (zero temperature coefficient current). The consequence is to reduce MOSFET power dissipation capability in lower ID zones of the SOA chart.
Measurement at DC, 100 ms, 10 ms and 1 ms establishes SOA capability. The 100 μs and 10 μs lines on this graph are theoretical constant power lines. They are realistic, as the Spirito effect is much less significant at higher currents and shorter pulse periods.
Reliable 100 μs SOA measurement capability has recently been achieved, so future data sheets can include 100 μs SOA lines based on measured data. It is now evident that the Spirito effect is apparent at 100 μs. Consequently, from 2016, some new MOSFET releases have a measured 100 μs SOA line in their data sheet SOA graph.
See AN11158 for further information.
The factors influencing the compliance of the MOSFET with the data sheet SOA graph are:
- the uniformity of the MOSFET cells across the active (trench) surface of the die
- the integrity and uniformity of the die attachment (the solder layer between the die bottom (drain) surface and mounting base)
Cell uniformity must be good for the MOSFET to work. However, cell uniformity can never be perfect and there is always some variation between cells.
The integrity of the soldering to attach the die must be good without voids or die tilt. If not, the local (junction to mounting base) thermal impedance varies with location across the die. It gives uneven cooling. Uneven die surface cooling may be due to either or both of the factors stated. However, the consequence is the same i.e. SOA non-compliance with the data sheet graph.
In production, linear mode power pulse tests are used to stress the MOSFET thermally. If the die cooling is not sufficiently uniform, hotspots can form and the device parameters can change more than expected. A decision to reject parts can be made based on the results.
While all Nexperia MOSFETs can be used in linear mode operation, some Nexperia MOSFETs are designed specifically to be used in linear mode. The device description in the data sheet states that the device is suitable for operation in linear mode. To determine the suitability for operation
in linear mode, perform a thorough analysis of the SOA graph. This analysis includes derating the SOA graph for junction temperatures above 25 °C. The naming convention indicates that the MOSFET is designed for linear mode applications.
Even if a MOSFET is intended for use in linear mode applications, the part must not be operated outside its SOA. Post 2010, all Nexperia MOSFETs have a measured SOA characteristic. The limit of linear mode capability on Nexperia parts is shown in the SOA characteristic. As a result, the boundary of what is safe is established via measurement rather than calculation. The Spirito capability limit is shown in the SOA characteristic.
In general - Yes, but Nexperia Trench MOSFETs are designed to suppress this effect. The trench structure, unlike planar, can be very easily designed to suppress parasitic turn on of the BJT. For new Nexperia MOSFET technologies, the failure mechanism is thermal, which represents the limit of achievable UIS performance. In the trench case, a design feature in the source contact effectively short circuits the base-emitter of the parasitic BJT. In older planar technology, the shorting of base to emitter of the parasitic bipolar is not as effective. It is due to the longer path length in the n and p regions.
All MOSFETs are susceptible to failure during UIS. It depends on whether the MOSFET Tj reaches the intrinsic temperature of silicon. Furthermore, if the parasitic BJT is triggered, they can fail even earlier. It is because the BJT can be switched on relatively quickly but is slow to switch off. Current can then crowd in a certain part of the device and failure results. Newer Nexperia trench technologies are less vulnerable to triggering of the BJT than planar designs.
The base emitter path in the silicon design is designed to minimize the risk of triggering the parasitic BJT.
UIS testing is a fundamental part of Nexperia's defect screening procedures. It is applied to all devices. The test is designed to increase the junction temperature to Tj(max).
Devices fail at the thermal limit. At the thermal limit, the silicon becomes intrinsic and blocking- junctions cease to exist. It is considered to be the only UIS-related failure mechanism in our devices.
Avalanche current versus time graphs are based on conditions that take a device to Tj(max) and therefore, our ruggedness screening covers them. All Nexperia MOSFETs are ruggedness tested during assembly and characterized during development. The graphs are accurate and provide the worst case capability of the device to ensure reliability.
A temperature rise model is used, which is shown in AN10273 Power MOSFET single-shot and repetitive avalanche ruggedness rating.
No. The repetitive avalanche ratings are lower than the single pulse rating. Refer to the product data sheet for the device capability. Refer to AN10273 Power MOSFET single-shot and repetitive avalanche ruggedness rating.
The device can sustain small amounts of damage with each avalanche event and over time they can accumulate to cause significant parametric shifts or device failure. Nexperia has performed research into this area and provides the repetitive ratings in the data sheet. See also Nexperia Application Note AN10273 Power MOSFET single-shot and repetitive avalanche ruggedness rating.
There are two failure modes: current (parasitic BJT turn-on) and thermal. Cell density has implications for these failure modes.
Example - A device has an avalanche event once in two months so how many cycles of such an avalanche frequency can the device sustain? This question relates more to quality and reliability but it is important nonetheless.
For the answer to this question, refer to Section 2.4.3 of AN11158 and all of AN10273.
The current specified in the avalanche graph should not be exceeded. It is restricted to the DC rated current. The device factory test defines the limit which is guaranteed for the device.
The avalanche rating is modeled first and the results are then verified by testing to destruction. The test circuit used is similar to the one defined in JESD24-5. For SPICE modeling, the reverse diode characteristics can be defined and modeled. By adding an RC thermal model of the Zth characteristic, it is possible to estimate the Tj of the device.
The repetitive line is the line for a start temperature of 170 °C. It is because it predicts a temperature rise of 5 °C which is the maximum permissible rise from any starting temperature (see AN10273). It also corresponds to 10 % of the single-shot current using the same inductor value.
The capacitive dV/dt turn-on is strongly circuit dependent.
If the dV/dt across the MOSFETs drain to source is too high, it may charge CGD, which is the capacitance between drain and gate, inducing a voltage at the gate. The gate voltage depends on the pull-down resistor of the driver based on Equation (4).
In some bipolar drive circuits, such as emitter follower derived circuits, the problem is increased. It is because the driver cannot pull the gate down to 0 V and has approximately 0.7 V offset.
It is also important that the driver is referenced to the MOSFET source and not to signal ground, which can be significantly different in voltage.
The ratio of CGD to CGS is a factor but a good drive circuit is the critical factor.
Even if a VGS spike is present, it is safe for the MOSFET as long as the dissipation is within thermal limits and MOSFET SOA limits.

Nexperia MOSFETs are designed with a high threshold at high temperatures and we check VGS threshold at 25 °C is within data sheet limits. Logic level devices are designed and guaranteed to have a minimum threshold voltage >0.5 V even at 175 °C.
It is usually measured in a half-bridge test circuit. It is a measure of the device dV/dt during body diode reverse recovery. This data is not normally published in the data sheet. This dV/dt is in practice the highest dV/dt the device experiences.
High dV/dt can induce glitches onto the gate of the MOSFET. A snubber can help to reduce dV/dt and the magnitude of the VDS spike if significant. The ratio of Coss at low VDS compared to Coss value at high VDS is an indicator of the non-linearity of Coss. A very high ratio can indicate that the device can generate a high dV/dt. Gate driver circuit design can reduce the gate glitch. The ratio of QGD to QGS and the gate threshold voltage can be used to indicate the susceptibility of the device to gate glitches.
In theory, all MOSFETs are.
Soft recovery does reduce the dV/dt. Although dV/dt is not an issue for the MOSFET, a lower dV/dt is better for EMI, voltage spikes and crosstalk. The design and manufacture is very specialized, involving proprietary information.
At high temperatures, it is easier to trigger a parasitic bipolar as its VBE reduces. But if the BJT is effectively shorted out and current diverted away from it, then it is not an issue.
The aim is to obtain a dV/dt value to check if parasitic BJT turns on, leading to device failure. It is impossible to measure the characteristics of the parasitic bipolar transistor as its terminals cannot be accessed independently of the MOSFET terminals. A parasitic bipolar transistor is always created when a MOSFET is fabricated.
It is sometimes referred to as gate bounce. MOSFETs have internal stray capacitances coupling all three terminals and the gate is floating. The capacitors are inherent to the internal structure of a MOSFET.
CGD and CGS form a capacitive potential divider. When a voltage appears across the drain and source of the MOSFET, it couples to the gate and causes the internal gate source capacitor to charge. If the voltage on the gate increases beyond the MOSFET's threshold voltage, it starts to turn back on which can cause cross conduction. The ratio of the capacitances CGD and CGS determines the severity of this effect.
If improved thermal resistance is required, vias can be added to the footprint. The effect of adding vias is discussed in Section 3.5 of AN10874.
We do not perform any HV isolation tests on any automotive MOSFETs or specify any HV isolation parameter in our data sheets. Insulation testing is only applicable to TO-220F packages (Nexperia SOT186A)
Environmental conditions: 4-layer FR4 board at 105 °C ambient temperature.
Although it is possible to reduce efficiency, other factors become the constraints.
There is a strong similarity between the data sheet characteristics and the Nexperia SPICE models at 25 °C. It is especially true for transfer curve, RDS(on), diode characteristic, and gate charge. The SPICE model also accounts for the package parasitic resistances and inductances.
The SPICE models provided by Nexperia are generated from measurements performed on a sample of devices. Several parameters such as transfer characteristics, output characteristics
and gate charge are used. Values for parasitic package impedances and the data sheet maximum RDS(on) value are combined to produce a model that emulates the behavior of the sample MOSFETs.
- It is important to note that the SPICE models generated by Nexperia:
- represent typical parts that can be found within the production distribution.
- are set close to the maximum RDS(on) of the part without adversely affecting the other model parameters.
- are only valid for Tj = 25 °C.
Customers wishing to do design validation using a SPICE model, are advised to proceed with caution given the information provided above. Nexperia encourages designers to perform Monte Carlo simulations and use tolerance stacks in their simulation design. These factors permit part to part variation of their whole system to be accounted for.
Nexperia can advise on what reasonable levels of tolerance on key parameters for the MOSFET would be.
Drift engineering is optimizing of the drift region between the bottom of the trench and the epi/ substrate interface (light green area). The drift region supports most of the drain-source voltage in the off state. The purpose of drift engineering is to reduce the resistance of the drift region while maintaining the drain-source breakdown voltage V(BR)DSS capability.
Reduced cell pitch generally results in lower resistance and higher capacitance. The goal of each new generation of MOSFET technology is to reduce RDS(on) without a large increase in capacitance that usually accompanies reduced cell pitch. Reduced cell pitch also reduces SOA capability (linear mode operation) but improves avalanche capability.
Shorter channel gives a lower RDS(on) and a lower CGS capacitance simultaneously. It has higher leakage current and the transfer curve (ID versus VGS characteristic) becomes more dependent on VDS. It is also observed in the output characteristics.
Thick bottom oxide refers to gate oxide at the bottom of the trench. It is made thicker than the gate oxide at the side of the trench. It acts as a thicker dielectric between the gate and the drain resulting in a much lower CGD value.
Nexperia continues to supply older products where the volumes of manufacture are economically viable. The sales price margin is commercially viable and there are no manufacturing reasons which prevent manufacture.
A Discontinuation of Delivery (DoD) document notifies key customers (including distributors), when a part is planned to be withdrawn. It allows customers to make arrangements to buy sufficient products for future requirements and if necessary qualify alternative products.
We have a detailed application note on this subject, AN90011, please refer to this for any EMC related concerns.
The key parameters are the gate oxide breakdown voltage and the gate input capacitance (Ciss). JESD22-A114 specifies the ESD Human Body Model test arrangement and results assessment criteria.
This formula estimates the ESD capability:
Vesd (HBM) = 16 × VGS(max) × Ciss (nF)
Yes. The ESD rating relies upon Ciss and gate oxide breakdown voltage. As Nexperia improves technology and the levels of quality and reliability also improve new generations tend to have stronger gate oxides. However as we improve our switching figure of merit (QG × RDS(on)), now for the same RDS(on) new technologies will have lower Ciss and therefore lower ESD rating.
In order to effectively screen MOSFETs with weak gate oxide and achieve <1 ppm quality levels, Nexperia uses special test techniques which involve accurately measuring the gate-source leakage behavior. Adding ESD protection networks means that it becomes very difficult to measure the gate-source leakage characteristics of the gate oxide because the ESD protection network will have a significantly higher leakage current. This means we cannot screen out weaker oxides and will result in a higher field failure rates. Furthermore, adding protection networks results in higher production costs. ESD protection networks are therefore only used where necessary.
Generally, for larger MOSFETs with good gate oxide quality and relatively high Ciss there is no need for ESD protection, as long as these are being mounted onto a PCB in a controlled ESD environment. For special applications where the MOSFET would be subjected directly to ESD in a finished product such as a lithium ion battery module or a power or signal port then on-chip ESD protection may be required to meet IEC 61000-4-2 or other ESD test specifications. Some very small MOSFETs from Nexperia may require on chip ESD protection networks in order to allow handling (such as NX3008NBKW), even in well controlled manufacturing environments.
The fundamental relationship between drain leakage current and temperature is exponential in form. The data sheet gives maximum values of IDSS at Tj = 25 °C and 175 °C.
Although these two parameters reference the voltage rating of the part, they look at different characteristics of the product. Drain leakage current (IDSS) is the current which flows when VDS equal to the rated voltage is applied. The test checks that the current is below the limit.
The breakdown voltage of a device V(BR)DSS is the VDS required to cause a drain current of 250 μA to flow. In practice it is slightly higher than the rated voltage of the device and the actual voltage varies for the same nominal type due to manufacturing variations. The minimum V(BR)DSS stated in the data sheet is the rated voltage. Breakdown voltage looks at the characteristic of the part when it is in avalanche. The mechanisms causing leakage current and avalanche current are different.
Nexperia has a high degree of confidence that this scenario would be OK even in the worst case. However, it cannot be 100 % guaranteed by a production test at 25 °C.
The following principle could be applied to any Nexperia MOSFET technology at any breakdown voltage rating. In the data sheet, the values for minimum drain-source breakdown voltages are specified at -55 °C and 25 °C. The correlation between V(BR)DSS and temperature is approximately linear over this range. Therefore, a straight line can be plotted at Temperature (-55 °C and 25 °C) versus V(BR)DSS (at -55 °C and 25 °C).
For example: a 40 V Trench generation 6 part, has a V(BR)DSS at -55 °C of 36 V and 40 V at 25 °C. Using linear interpolation, gives a V(BR)DSS of 36.75 V at -40 °C.
The answer to this question is not simple - there are several factors which would affect the ID value.
Unfortunately, Nexperia cannot supply values for these capacitances at the extremes of the MOSFET operating temperature range requested. It is due to the limitations of our parametric test equipment. However, we can comment on how these capacitances vary with temperature and the MOSFET terminal voltages.
Ciss is the input capacitance formed by the parallel combination of CGS and CGD, and CGS dominates. CGS is formed across the gate oxide so it does not vary significantly with
temperature or the MOSFET terminal voltages. As CGS depends on gate oxide thickness and other defined die feature dimensions, it should not vary much between samples.
Crss is the reverse transfer capacitance which is essentially the gate-drain capacitance (CGD). It is formed across the MOSFET body diode depletion layer. This layer becomes thicker, as the reverse voltage (VDS) across it increases. Crss increases as VDS decreases. Crss has a greater variability than Ciss because it depends on the body diode depletion layer.
Coss is the output capacitance formed by the parallel combination of CDS and CGD. The drain- source capacitance (CDS) also dominates this capacitance. It varies with VDS in a similar way to Crss varying with VDS and it has similar variability to Crss for the same reasons.
It has been observed that switching losses only slightly increase at Tj(max), in the order of 10 %, since the capacitances only marginally change. Other factors can influence switching behavior, especially where the gate driver current capability changes significantly with temperature. The depletion layer thickness varies in proportion to the square root of the absolute temperature in K and it affects Crss and Coss.
Worst case values of minimum and maximum VGS(th) should be used for design purposes. They are given in the data sheet Characteristics.
The measured RG value is in the range of 1 Ω to 3 Ω and it does not vary significantly with temperature. In our general MOSFET characterization, it is presently not possible to test RG over the temperature range.
The minimum current that is expected at a VDS of 0.1 V can be calculated from the maximum (175 °C) RDS(on) value (26 mΩ).
The drain current that flows with these conditions is 0.1/0.026 = 3.846 A. The maximum die temperature is the critical factor. Do not allow it to exceed 175 °C.
However, if the RDS(on) is not at the top limit of the value range or the die temperature is lower, it is lower. As a result, the corresponding drain current is proportionately higher.
The maximum RDSon is 11.5 mΩ at Tmb = 25 °C. The maximum die temperature is likely to be higher than 25 °C in most applications.
If the mounting base temperature is maintained at 100 °C or less, the (fully ON) MOSFET can safely carry a continuous current up to 35 A.
The (fully ON) MOSFET can also sustain a current pulse of 204 A for a period up to 10 μs.
The ratings given on the data sheet are for each individual MOSFET in this device.
Although there are two MOSFETs housed within the package, they are fully electrically isolated from each other.
However, as the MOSFETs share a common package, there is a small amount of thermal coupling between the two MOSFET dies through the plastic package material. The heat generated by the power dissipated in one MOSFET increases the temperature of the other, even though the other may not be dissipating power. In an application, there is also an external thermal coupling path via the PCB to which the device is mounted. In practice, it is the main thermal coupling mechanism between the two dies.
To guarantee long-term reliability, it is very important that the junction temperature of either of the dies is never allowed to exceed 175 °C.
The individual MOSFET mounting bases are the main exit routes for heat generated in the dies. In practice, the mounting bases are soldered to copper pads on a Printed-Circuit Board (PCB). They provide the electrical connections to the MOSFET drains and heat sinking. Both MOSFETs in the package should operate at their rated power/current when their mounting bases are maintained at 25 °C. However, it is very difficult to achieve in practice and de-rating must be done in most cases.
Data from a T9 MOSFET family device BUK7J1R4-40H is considered but the principle can be applied to T6 devices also. The plateau voltage in the gate charge characteristic is the horizontal portion of the Gate-source voltage as a function of gate charge graph (see Fig 13. in datasheet); and is related to the transfer characteristic (Fig. 8).
The plateau voltage is around 4.25 V typical for a current of 25 A. This corresponds to the value in the transfer curve, also for a typical device. So at -55 °C then the plateau voltage will be 4.35 V and at 175 °C it will be 3.9 V for a typical device.
When considering a “worst case” device then the spread in gate threshold VGS(th) needs to be considered. It is assumed that the gain (transconductance) of the device is not affected by the same process related reasons which affect VGS(th). The transfer curve for a typical device would be shifted along the VGS axis according to the delta in the VGS(th).
The plateau voltage at the 25 A test condition would be 3.65 V for minimum VGS(th) and 4.85 V maximum VGS(th).
Consider a specific example such as BUK9K52-60E. See table 1 in the datasheet for capability.
The key point is the Ptot of 32 W. This is per die at data sheet conditions which assume that the mounting base is maintained at 25 °C. The maximum DC current allowed in each device would be
16.04 A, based on RDSon of 124.3 mΩ (VGS= 5 V) at 175 °C.
If both devices in the package are considered then the total power dissipation when both mounting bases are maintained at 25 °C is 32 W x 2 = 64 W. This only applies when the mounting bases of the devices are maintained at 25 °C (using an infinite heatsink). The power capability will decrease as the mounting base temperatures increase such that Tj does not exceed 175 °C. Consequently the current will decrease as shown in the Fig 2 in datasheet of ID vs Tmb, if the mounting base is maintained at a different temperature such as 125 °C, the current rating would be 9.26 A.
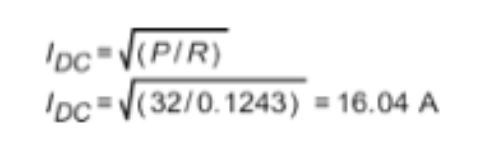
FIT (Failure In Time) is commonly used to express component reliability. It is defined as the number of failures occurring in 1 × 1000000000 hours (1 billion hours).
At any elapsed time (t), the reliability (R) of a group of operating semiconductors is: R(t) = (no - nf)/no
Where:
no is the original sample size and nf is the number of failures after time t.
Over the standard time of 10^9 hours, it approximates to F = (1/no)*(nf/t)*1000000000.